
Weld a 10 foot tube on the 1/4" plate and then wiggle the end of the tube. Weld the 1/4" plate to the thin sheet metal. What it doesn't address is how the load is transferred to thin sheet metal. My input on the 1/4" plate is that the 1/8 plate was viewed as insufficient to carry the load. What? That didn't help either? Don't ya hate the guys that use big words?įEA is a computer modeling program that allows you to simulate stress loads and calculate the stress through the part. If you have something like a roll cage and try to figure out the possible paths of stress it isn't something you can do on a spreadsheet, much less in your head.įinite Element Analysis (FEA)) is a numerical technique for finding approximate solutions of partial differential equations (PDE) as well as integral equations. If you have a single post and put a 50 pound weight on top you know what the load on the bottom of the post is going to be. In addition to the straight plate could you model Larry’s idea with a 30 or 60 degree beveled edge? FEA or anything else that brings a better understanding is greatly appreciated. If good data showed my concerns were wrong I would be at peace.
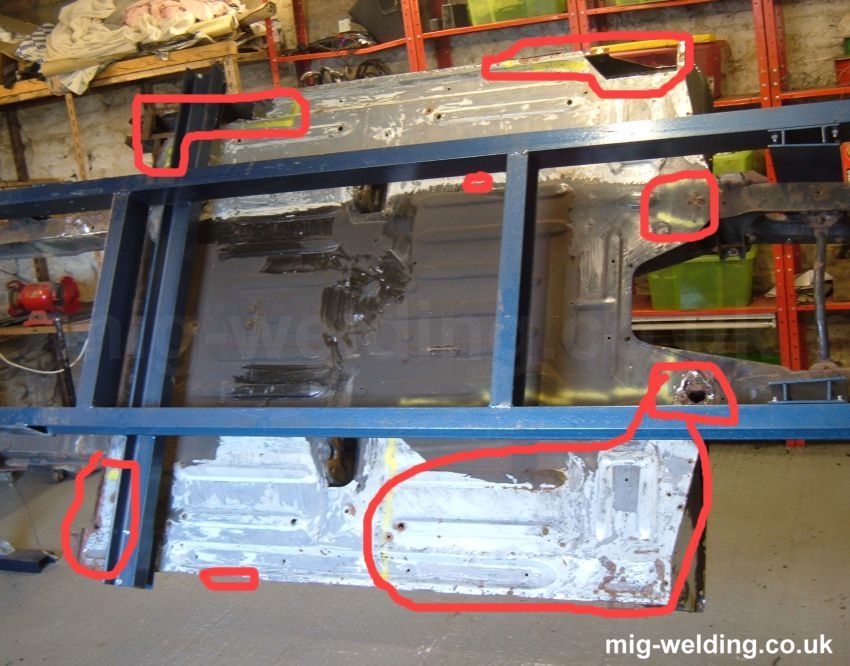
I am just concerned, but I lack the technical or engineering data to discuss this with the SCTA principals. I am not saying the rule is unfounded or without merit. However, sometimes the lack of technical information raises questions. In our litigious society I can certainly understand, respect, and support that position. SCTA does not share publicly any technical analysis. Neither car is mine but I have the same model and have measured the pan thickness in those areas. Welding ¼†thick plate to thin sheet metal begs a few questions. The cars in the pictures have the ¼†plates welded to 0.035†sheet metal floor pans. (Edit) I am having trouble getting the pictures posted. I will try to model up a few plates and upload them later. Somewhere I have a video of a Mustang going on its lid and you can see the cage feet punch through the floor. All the attachment points (footings) were. Also, because it is a small car the cage mounted not on the floor, but on top of the rocker panel structures. Of course, it was to help stiffen the chassis so it picked up the front suspension points and the rear sub frame mounts. The last car I caged, Miata open top had 20 points of attachment to the car. IMHO, the materials used are secondary to the design and attachment of cage. It is my understanding that the lesser material will deform and stay attached to the sheet steel without tearing. The issues I have seen are not the roll structure penetrating the foot, it is the foot tearing out the flooring under it.
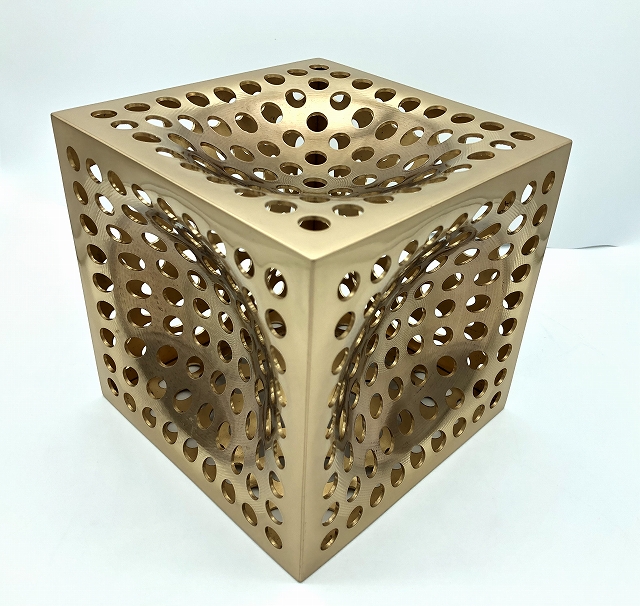
The trend has been to go from 1/4" plates down to. Not having witnessed the failures around LSR, I can only comment on SCCA cars. This latter method would avoid the issue of concern about the strength of attachment of the thin doubler plates, and give more inches of perimeter to the base plate and a more ductile edge which might give under extreme impact rather than trying to cut a disk of sheet metal out of the body work.
#Floor pan sheet metal yellow bullet forums full
I see no reason why the 1/4" base plate could not be full 1/4" thickness for the required surface area with a wide bevel at perhaps 30 degrees beyond that so the actual weld occurs between similar thickness materials. There might be some concern about the strength of attachment of the doubler plate, so options include photographs taken during fabrication showing the matrix of plug welds hidden under the 1/4 inch plate, or use backup bolts to provide redundant attachment.Īfter that thought had passed I realized that the rule does not specify the edge shape on the 1/4" plate. That way the 1/4" plate has a much more difficult time trying to cookie cutter through the body structure as it has to shear 2 pieces of thin sheet metal rather than a single layer of sheet steel. Say for example you have a 6" square 1/4 thick plate, put it on top of a 7" square piece of 16 gauge that is stitch welded and plug welded to the sheet metal structure. The debate about how you weld a 1/4 inch thick plate to perhaps 18 - 20 gauge sheet metal got me to thinking and my first thought was to put a sheet steel doubler on the sheet metal structure that is larger than the base plate of the roll bar. Comment regarding welding thick base plates to thin unibody structures.
